According to Kister [1] damage to tower internals is the number 3 on the top 10 causes of column malfunctions. High costs arise due to repairing costs and production downtime. Most of the destruction is caused by mechanical load, seldom a high temperature is the cause. The design of distillation columns and column internals is directed to the necessary separation performance. In contrast to that the mechanical layout of column internals is of subordinate interest and mostly done according to guidelines applying to stationary operating conditions. For example an industry standard is the differential pressure column trays have to withstand. The minimum differential pressure is in the order of 15 mbar and can be applied from both directions. Due to the enhanced competition most tray manufacturers design for this minimum load. Another industry standard is the vapor pressure drop over a tray which is in the order of 2.5 to 7.5 mbar. However these boundaries are only valid for stationary operation conditions and can be easily exceeded if the column is leaving the field of normal operation. Regarding the fact that the differential pressure is a quadratic function of the vapor flow, an increase of 50% vapor flow (beginning at stationary conditions with
DP=7.5 mbar) would already lead to a pressure drop which is beyond the standard design limit (
DP=17 mbar). For a better understanding of the dynamic behavior in this field of operation, experimental investigations were carried out on a pilot scale column. The column has a height of 4 m and a diameter of 0.1 m and is equipped with 16 sieve trays. The column is provided with differential and absolute pressure sensors and automated with Freelance2000 from ABB. A glass section gives an inside view on the events happening in the column. Additionally a measurement technique based on strain gages was developed, tested and implemented inside the column on the tray suspension to measure directly and online the mechanic load on a tray during operation [2]. Two important scenarios were chosen and experimentally investigated: a) Phase separation in reboiler causing first boiling delay and afterwards a violent boiling, producing a rapid upward flow b) Emergency pressure relief with an oversized relief valve causing a rapid upward flow In the presentation a summary of the experimental investigation will be given. Results concerning maximum differential pressure and maximum force on a tray, even lifting of trays after an operation failure will be shown. Measures and methods to prevent comparable incidents in the future will be suggested. [1] H. Z. Kister: Distillation Troubleshooting, New Jersey USA: Wiley-Interscience, ISBN-13 978-0-0471-46744-1, 2006 [2] D. Staak, J.-U. Repke, G. Wozny: Outflow conditions and strains on internals during pressure relief events on distillation columns, Prag, Pres Conference, 2006
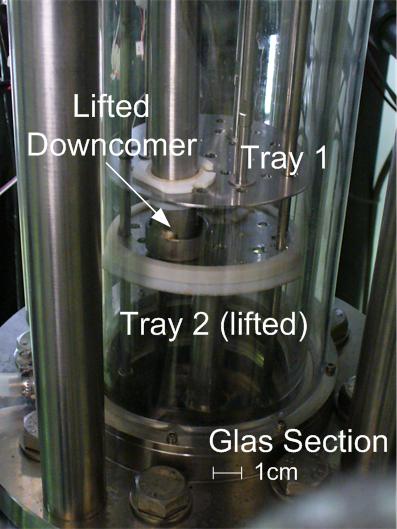